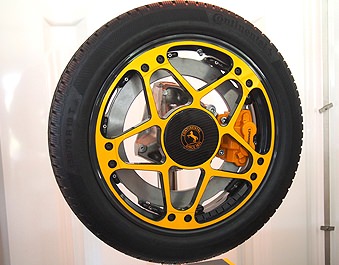
Europe’s Continental brand has come up actually re-inventing the humble wheel. The radical new wheel was unveiled by Continental before its official launch at the Frankfurt motor show in September.
The new wheel incorporates an aluminium brake rotor and the calliper into the overall construction, designed to solve or improve issues associated with the braking systems of EVs in particular.
By not using the more usual cast iron brake rotor, the new aluminium rotor is lighter and does not corrode. EVs usually have pitting and rust problems with their discs because the energy regeneration systems do most of the braking, meaning that the discs are not worked as hard.
The new wheel consists of the wheel rim, the wheel ‘spider’, a brake disc and calliper. In some ways this harks back to the wheel/drum combination of the Type 35 Bugatti’s.
The first examples use very large rotors inside the wheel rim with the brake calliper fitted inside the rotor, rather than on the outer edge, allowing the rotor to have a huge diameter compared to conventional systems.
“As this disc is corrosion free and we don’t have any relevant wear on the disc, this can stay the lifetime on the vehicle,” said Continental engineer Dirk Eser.
Simple physics would show that the larger rotor is more efficient and less pressure can be applied to the disc to achieve the same retardation as a standard (smaller) disc.
“There is still friction, but as we have reinforced aluminium, there is really no relevant wear, no wear that would force you to change the disc during the lifetime of the vehicle,” he said.
A disc that lasts the life of the car will be cheaper in the long run as cast iron rotors have to be replaced – sometimes as frequently as every two years – because they have been designed to be sacrificial.
“Definitely one of the targets is always to be lower in cost,” Eser said. “This is always the case. Where we will end up we will see.
“This is not just about a wheel. You’re creating an integrated system that also is included in the overall lifetime cost of the vehicle.”
Eser said he was confident the wheel would be chosen by a car manufacturer in the near future for mass-market manufacturing.
“With this part, it is quite promising,” he said. “We are starting to promote it and you will see in three or four years that this is going to launch into production.”
According to Eser, developments are continuing with the number of parts required reduced while still allowing for the different rates of expansion between aluminium and steel/cast iron.
Continental just looks as if they might have re-invented the wheel.